毎日どこかで触れられている四国の技術
大下勝二さん 四国化工機 http://www.shikoku-kakoki.co.jp
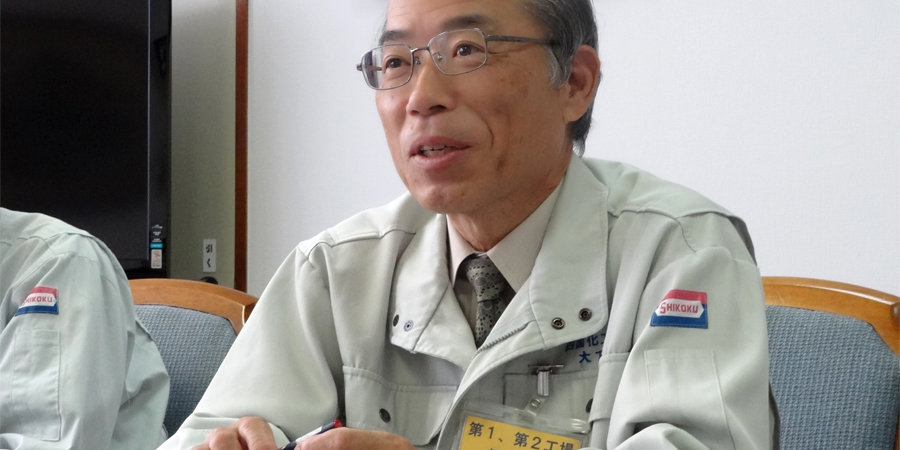
私たちが普段何気なく口にしている乳製品やジュース、インスタントラーメンなどといった容器に入れられている食品に四国の技術が使われていることをご存じでしたか?食品充填機製造大手で紙容器成形充填機では国内でも高いシェアを持ち、世界最高レベルの品質を誇る四国化工機を訪問し、長年、設計開発・品質管理に取り組まれてきた大下勝二常任監査役のお話を聞いてきました。
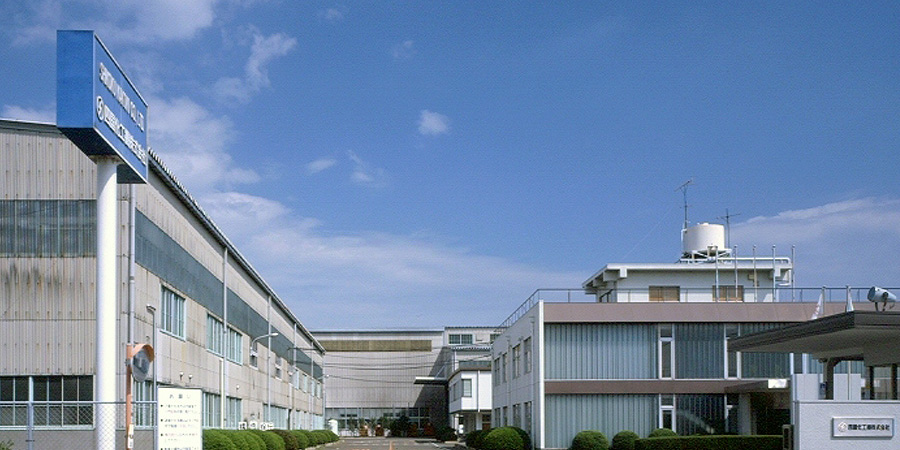
-もともとは、乳業関係の製缶・タンクの設計・製造会社でした。ちょうど50年前、1961年(昭和36年)の創業です。その後、次なる柱となる付加価値の高い製品として1967年(昭和42年)に大手乳酸菌飲料メーカーの主力商品のプラスチックボトル充填包装ラインを完成させたことにより念願の機械メーカーへの転身を果たしました。包装資材事業は、1972年(昭和47年)、シュリンクフィルムの製造・販売から始まります。
一方で、同時期に絹ごし豆腐自動製造機を開発したことを契機に、1973年(昭和48年)に自社で豆腐を製造・販売する事業を立ち上げるのですが、現在では自社ブランド「さとの雪」やOEM製品を1日40万丁製造する国内有数の豆腐メーカーになりました。
このように、「充填包装機器事業」「包装資材事業」「食品事業」の三事業部門で運営されているわけですが、現在の売上は約360億円になります。食品充填機製造大手で紙容器成形充填機では国内ナンバー1シェアを持っています。『三事業部門は、相互に切磋琢磨して相乗効果を高め、時代の変化を先取りした経営革新と、独創技術の開発で、常に市場の一歩先を歩み続けて、優良国際中堅企業として世界の食文化の向上に貢献する。』を経営理念に据え、「安全・安心・品質」の"ものづくり"を基本とした事業に取り組んでいます。
![]() |
![]() |
![]() |
多様なニーズに応える「充填包装機器事業」 | 最適のパッケージを充填機とともに企画・提案する「包装資材事業」 | 「食品事業」のノウハウが機械や包材にフィードバックされていく |
ちょうどそのころ、四国化工機が次なる開発のために大学卒の技術者を募集していたのです。当時は従業員135名程度で売り上げも16億円程度。そのときの総務次長が熱心に半年間毎週のように説得に来てくれて、「四国化工機であれば地元に帰れるし、第一線で活躍できるかな。」ということで転職を決めました。当時は、徳島に四国化工機という企業があることは知りませんでした(笑)。
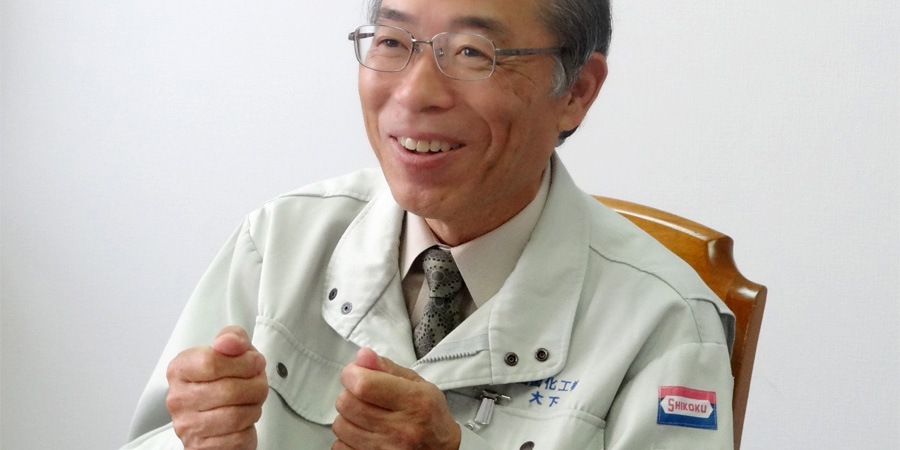
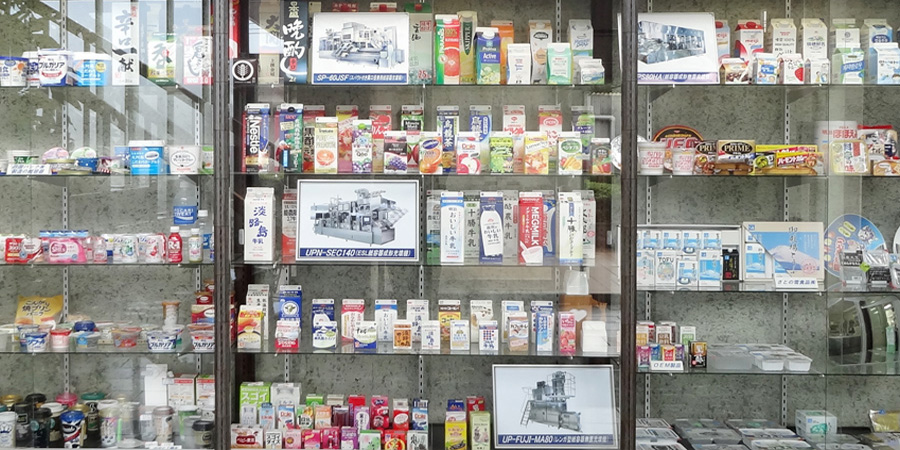
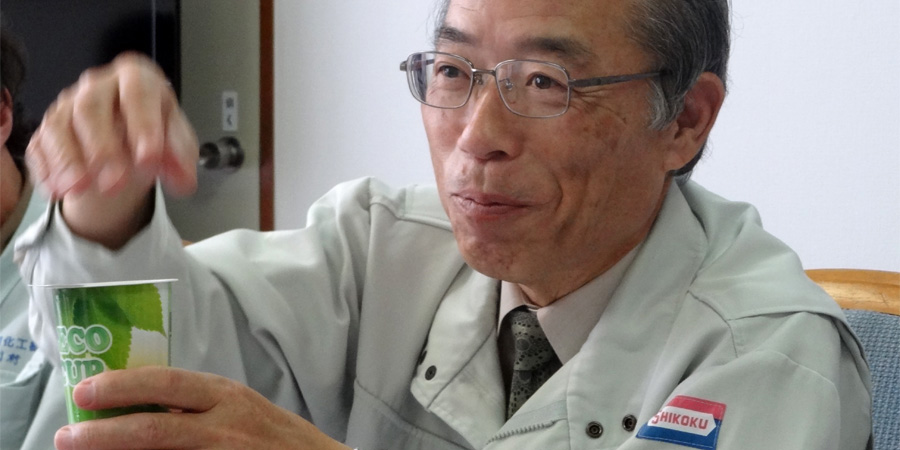
品質保証部長になる前だったのですが2000年(平成12年)に起きた大手乳業メーカーの食中毒事件を契機に消費者による商品に対する目は厳しくなり、飲料メーカーを含め乳業界に大きな転機をもたらしました。クレームにより製品回収を行った場合、回収に1製品1億円かかると言われますので、食品メーカーは品質管理を一層強化するようになりました。そして製品回収となった場合に、食品メーカーは充填機やタンクなどの設備メーカーに対して補償を求めるようになってきたのです。当社は基本的にその要求を受け入れていませんが、当社の製品に対するユーザーの目も格段に厳しくなりました。
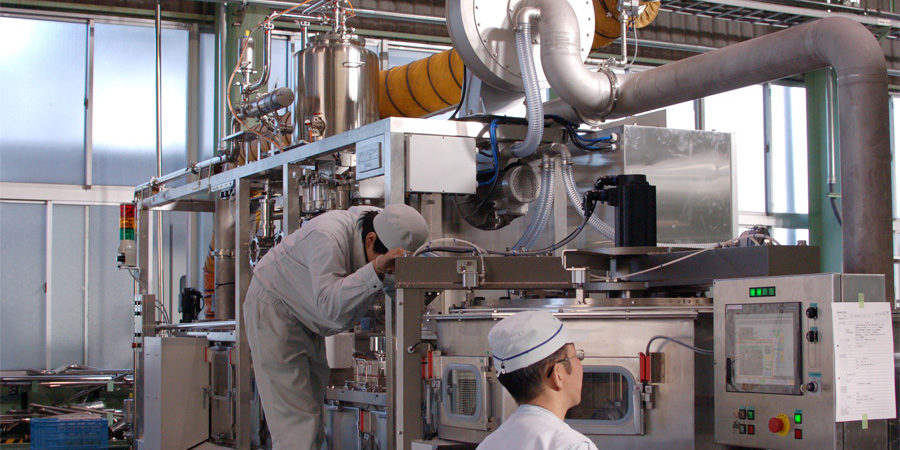
クレーム要因のほとんどは溶接に起因しています。
実は1990年代以前の充填機は鋳物製品を多く使っていました。しかし、1990年代に入ると中国から安い鋳物が日本に入ってくるようになり、国内の鋳物屋さんはどんどん止められていきました。そのため、当社の充填機に使っていた鋳物製品を溶接構造に切り替えざるを得なくなるんですね。そのときより、いろいろな溶接の不具合問題が発生し、毎年クレームに占める割合も大きなものでした。
当然、溶接構造の改善・改良に取り組み、溶接設計図面の見直し、協力会社の技術向上支援や勉強会などを実施してきましたが、件数的には減少してきているといえども、現状でも年間20件程度のクレームが出ています。当社は品質に対して強いこだわりを持ち、1992年(平成4年)に四国では2番目にISO9001を取得していますし、クレームの削減に対しても積極的に取組んでいます。
溶接製品自体、後で検査するしか方法がなく、それも外観検査が主体であり、非破壊検査など、いろいろな検査方法がありますが、今の検査では限界があると気付きました。
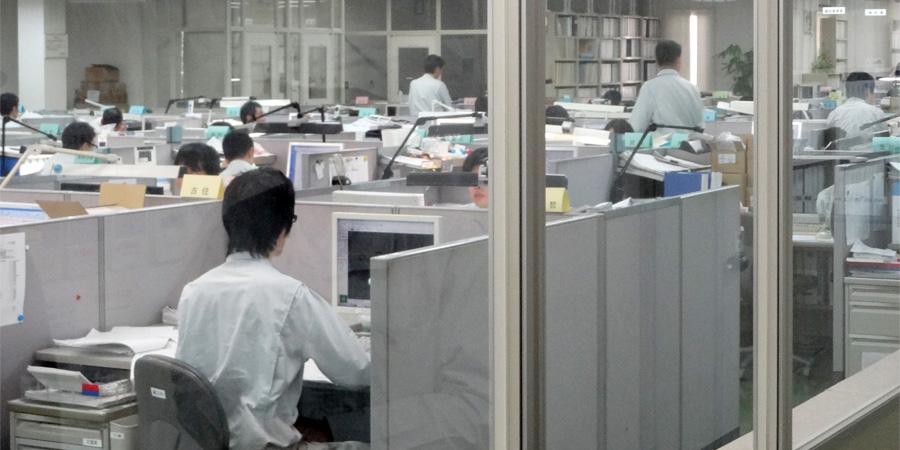
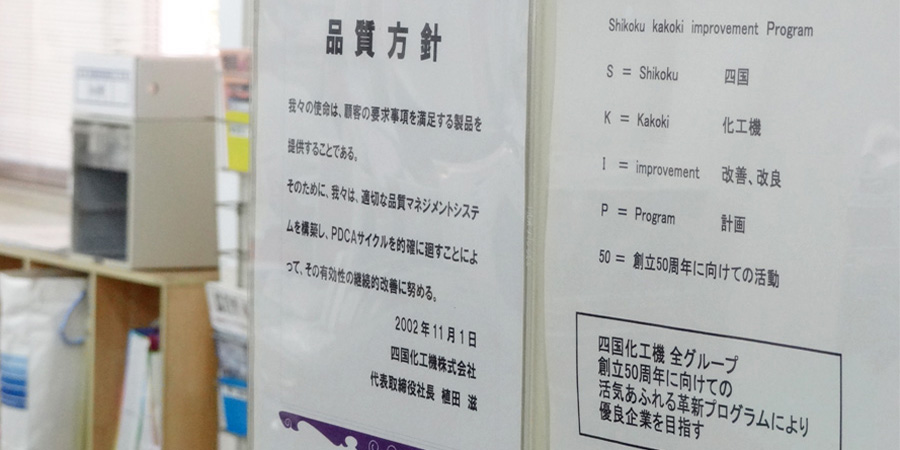
開発当初は当社製品の品質向上のためにと思っていたのですが、溶接技術の熟練者になるには10年かかると言われています。少子高齢化の時代において、数年間で高い技術レベルの習得が求められたので、このシステムは後継者の早期育成にも大いに役立つものと期待しています。
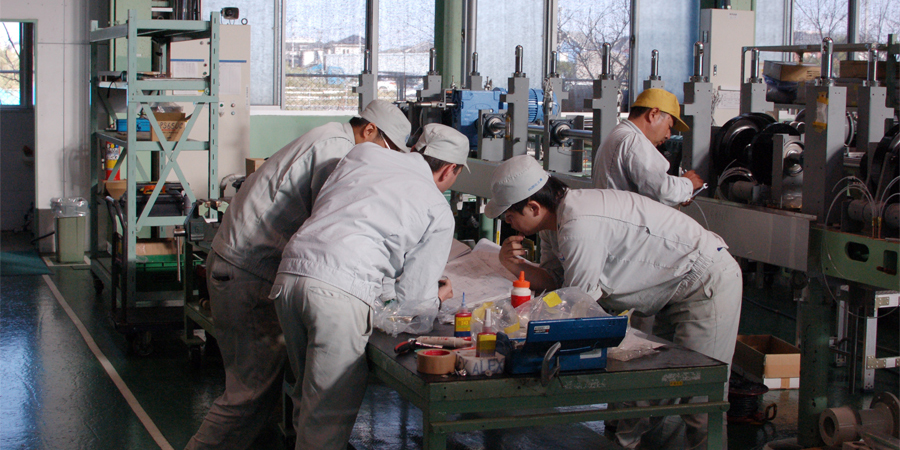
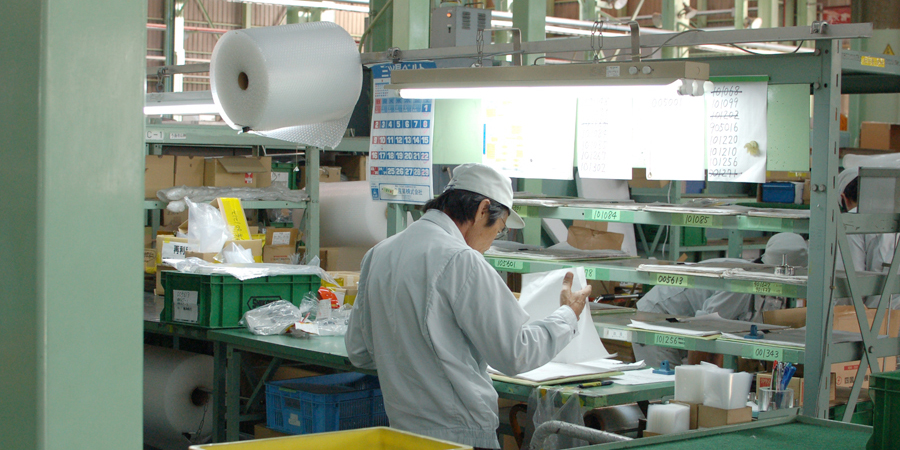
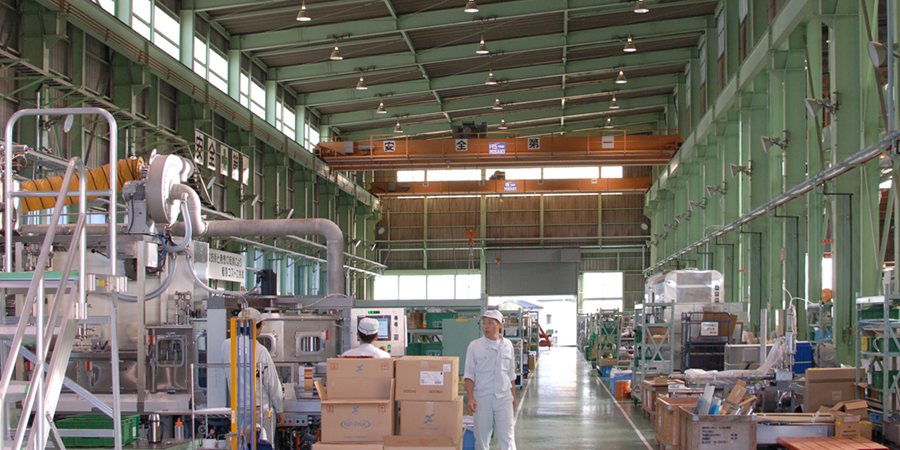
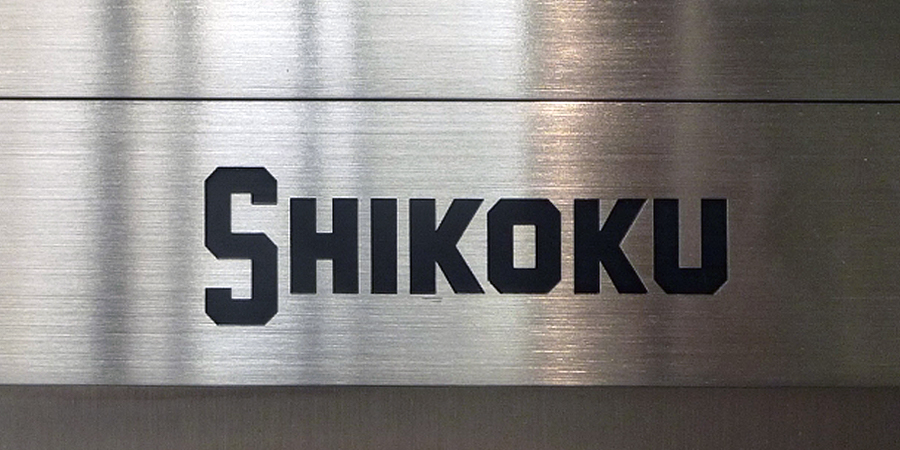
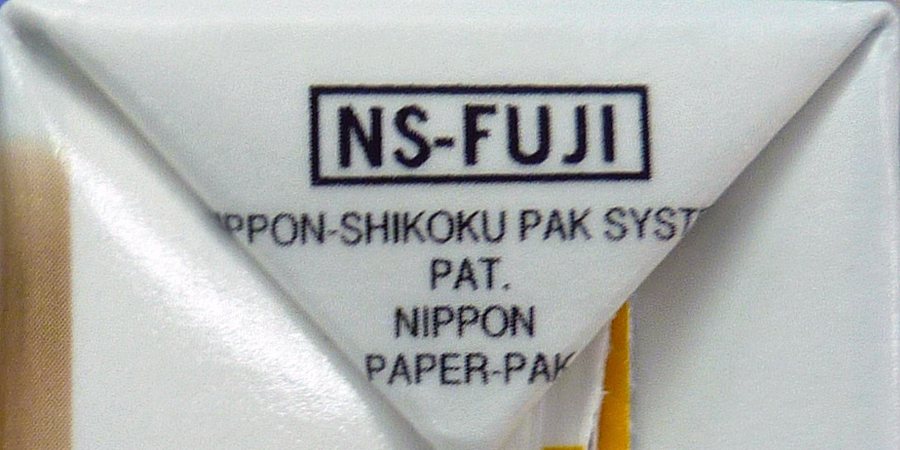
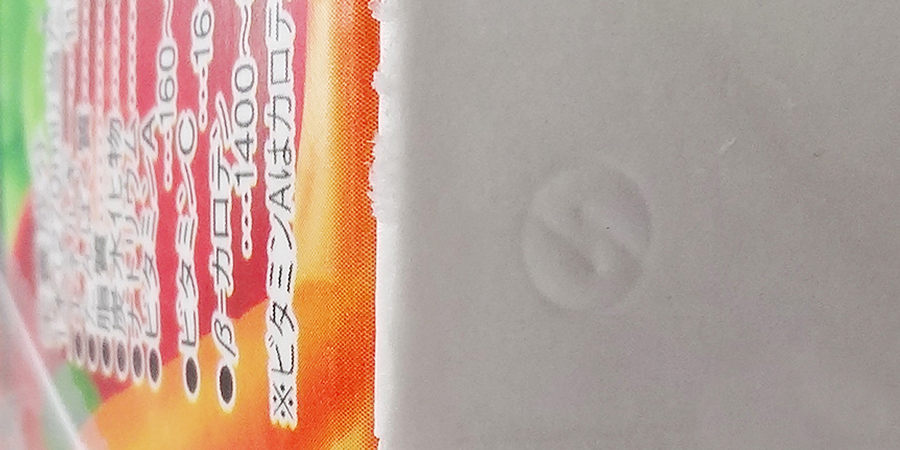
容器底面にこの印字やエンボス加工があれば四国化工機の充填機でできた製品 -四国の地で"ものづくり"をされることにこだわりを感じますが、協力企業さんはやはり四国地域が多いのですか。 大下さん -常に取引している協力会社は販社を含め80社以上あり、その内6から7割は徳島で、その他四国各県及び関西圏と近隣の企業で構成されています。
創業者である植田道雄名誉会長は地域密着という強い思いがあり、「協力会社にも仕事を切らさず守らないといけない。」という考えを強く持っています。1989年(平成元年)には協力会社とともに「共進会」というものも組織し、他には例を見ないほど積極的に生産技術研究会やセミナーを開催し、親睦を深めるための見学旅行などを年2回実施しています。
一方で、地域密着の観点から「すだちはちみつ」飲料を製造販売したり、豆腐製造過程から出る「おから」については、産学官連携プロジェクト「とくしまSOYくふう」を立ち上げ、おからの循環活用による商品開発もしています。
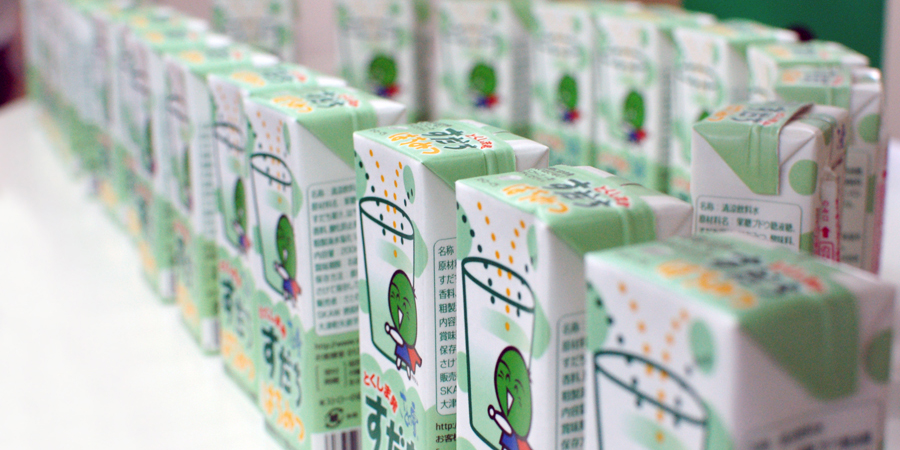
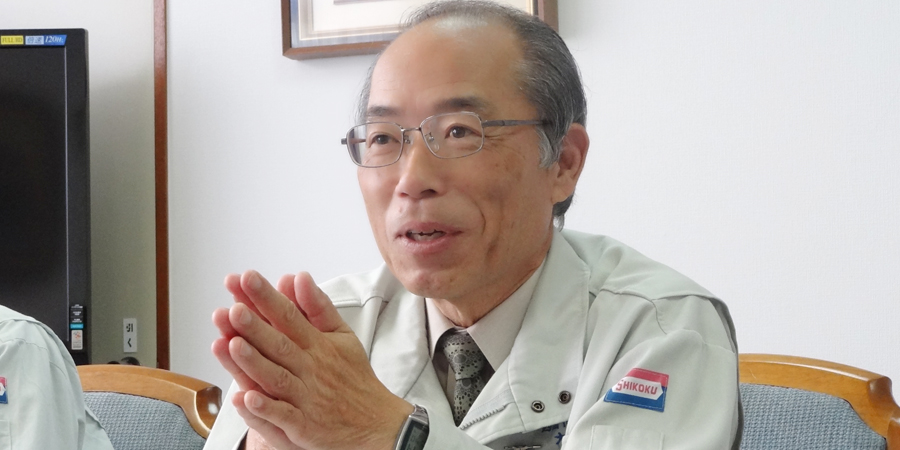